УПРАВЛЯЙТЕ ВСЕМИ ПРОЦЕССАМИ ДИСКРЕТНОГО ПРОИЗВОДСТВА НА КРУПНЫХ И СРЕДНИХ ПРЕДПРИЯТИЯХ С ЕДИНИЧНЫМ, МЕЛКОСЕРИЙНЫМ И СЕРИЙНЫМ ПРОИЗВОДСТВОМ (MES)
- Составы изделий
- Расцеховка
- Технологии
- Нормы изготовления изделий
- Продукция внешней поставки
- Заказы
- Оборудование
- Контрагенты
Управление утвержденной документацией на изделия
Разработка и планирование СТО
Управление производством СТО
Объемно-календарное планирование производства
Формирование производственной структуры изделия
Цеховое планирование
Расчет финансового плана и калькуляции стоимости изделия в части ТМЦ
Формирование и обработка потребности производства в ТМЦ
Диспетчирование производства на уровне сменных заданий
Учет ТМЦ на центральных складах предприятия
Учет и комплектование ДСЕ и ТМЦ в кладовых производственных подразделений
Учет готовой продукции и полуфабрикатов
Управление качеством покупной и изготавливаемой продукции
- Управление нормативно-справочной информацией
- Формирование производственного состава изделия и управление им
- Объемно-календарное планирование производства
- Запуск в производство изделия на основе даты выпуска и технологического маршрута изготовления
- Диспетчирование процесса изготовления входящих ДСЕ и изделия в целом – на уровне сменных заданий и данных с датчиков оборудования
- Управление качеством изготовления изделий
- Ведение учета полуфабрикатов и готовой продукции
- Формирование и обеспечение потребности производства в материалах и комплектующих
- Использование технологии штрих-кодирования и QR
- Ведение позаказного учета затрат на производстве и партионного учета
- Автоматическое отслеживание изменения НСИ и плановых показателей, учет изменений в производственном составе
- Учет товарно-материальных ценностей на центральных складах предприятия и в кладовых подразделений
- Сбор и хранение полной истории изготовления изделий – от поступления комплектующих до сдачи на склад готовой продукции c сохранением истории технологии изготовления
- Разграничение прав доступа к функциональным возможностям системы
- Настройка индивидуального интерфейса АРМ
Наличие масштабных внедрений
Наличие опыта интеграции с SAP, 1С, ГИС, НСИ, WMS, IIoT, SCADA, PLC, системами PDM/PLM
Независимость от зарубежных поставщиков ПО
за счет совмещения в одной информационной системе конструкторских, технологических и производственных данных обо всех изготовляемых на предприятии изделиях
за счет получения достоверной и оперативной информации о текущей загрузке ресурсов и состоянии работ по изготовлению каждой детали и сборки, вплоть до конечных операций
благодаря обеспечению прозрачности планирования и производственного процесса (концентрация на решении проблем вместо поиска виновных)
за счет точного планирования и оптимизации работы станков в соответствии с производственными планами, на основании реальной картины загрузки и ритмичности работы оборудования
с учетом изменений в конструкторской и технологической документации за счет отлаженного, контролируемого процесса ее корректировки
благодаря удобному интерфейсу для планирования таких работ
за счет формирования и распределения потребности в материальных ресурсах и снижения межоперационного пролеживания
Увеличение коэффициента использования станков с ЧПУ с 74% до 85% за счет:
- определения реальной картины загрузки и ритмичности работы оборудования
- контроля трудовой дисциплины персонала, работающего на станках
- фиксации простоев станков, их классификации и оперативного устранения проблем
Снижение времени простоя оборудования на 428 часов в месяц за счет:
- более точного планирования загрузки станков в соответствии с планами
- определения «проблемных» точек производства
- оптимизации загрузки оборудования
Сокращение оборачиваемости запасов на 36,7% за счет:
- распределения потребности в ресурсах
- формирование запасов к определенному сроку (just in time)
- снижение межоперационного пролеживания
Потенциальное увеличение портфеля заказов на 10% при неизменном парке за счет:
- оптимизации мощности производственного кластера
- понимания возможностей производственной нагрузки
- перераспределения приоритетов производства
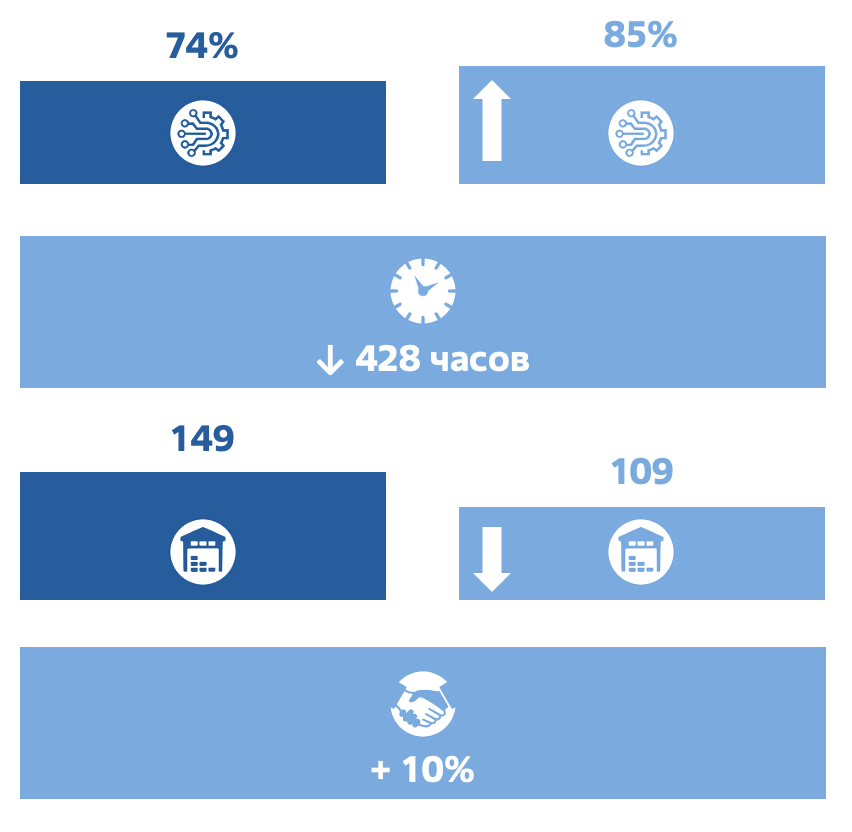